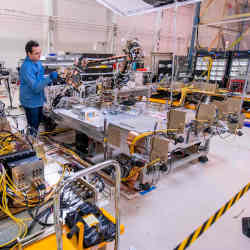
If a satellite in Earth orbit runs out of fuel or malfunctions, it becomes a serious threat to other satellites. Without enough fuel to keep it in its assigned orbital position or maneuver accurately, it can collide with other satellites, putting them out of action and creating hazardous space debris. What is really needed is a space-based equivalent of a tow truck, one that can visit and robotically refuel or repair satellites.
However, such a technology has not been available.
This is all set to change next year, however, when the U.S. Defense Department’s Defense Advanced Research Projects Agency (DARPA), working with military contractor Northrop Grumman and the U.S. Naval Research Laboratory (NRL), hopes to launch just such a spacecraft for the first time. The RSGS (Robotic Servicing of Geosynchronous Satellites) space vehicle will be the first general purpose “servicer” satellite, one designed to rendezvous with a troubled satellite and use two precision robot arms to capture and repair/refuel it in Geostationary Earth Orbit (GEO).
At some 35,800 km. (more than 22,000 miles) above the Earth, satellites in GEO hover over a fixed spot on the ground, enabling them to deliver 24/7 the valuable services on which people depend, like TV, Internet, telephone, global positioning, and weather, as well as remote sensing and military spysat data.
How will DARPA’s robotic spacecraft perform its cosmic choreography without colliding with its target satellite and making its own shower of hypersonic debris? We asked William Vincent, RSGS program manager at NRL, whose team is developing the onboard algorithms and robotic arms for the spacecraft, how they are doing it.
What’s the overarching ambition with RSGS? Is NRL developing the robotics for just one, or whole platoons of servicer robots?
Vincent: The robotic payload NRL is developing for the RSGS program is initially for a single servicing vehicle, but we certainly hope the program succeeds at transforming space servicing operations and demonstrating its benefits in such a way that multiple RSGS servicing vehicles will be needed to meet demand.
Does GEO-to-Earth communications latency mean the servicer spacecraft will have to be directed autonomously? If so, how can it avoid the crashes autonomous vehicles and unmanned aerial vehicles (aerial drones) have experienced?
Ground control is used for most of the mission, but you are correct that autonomy is required during the final grapple phase due to comms latencies to the ground. Unlike autonomous cars and aircraft, autonomous robotic grapple occurs under a well-controlled set of conditions. We’re undertaking extensive ground testing and analysis to verify the reliability of the autonomy before mission operations start.
In geostationary orbit, your target satellites are moving at 3 kilometers per second (6,700 m.p.h.). What types of onboard sensing systems will the servicer need for a collision-free rendezvous ?
While orbital velocities are high, the relative velocity that the robotic payload experiences with respect to client spacecraft is very low; less than 1 centimeter per second (0.067 m.p.h). To ensure safety during robotic grapple operations, ground operators will verify all systems are performing correctly prior to commanding an autonomous grapple sequence.
How do the servicer’s algorithms ‘know’ what’s happening? What are its sensory inputs?
Robotic payload algorithms onboard use both machine vision to properly align the grapple tool, and force/torque sensing in the robot arm to detect contact. At contact, a compliance control algorithm does two things: it modifies arm behaviors such that contact forces are minimized, and also controls the grapple tool so the servicer is safely attached to the client.
As NRL is ostensibly a naval-oriented lab, do you have ways to simulate these complex, robotic space operations?
NRL has extensive robotic and spacecraft test facilities, and we are developing tools that simulate conditions that can’t be created on the ground. Unlike many space robotic systems, the RSGS robotic arms are designed to operate in Earth’s gravity, and that allows us to verify many of the robotic payload functions and performance characteristics on the ground.
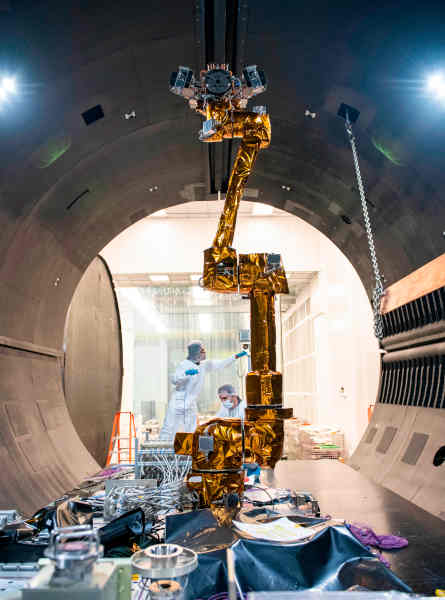
Satellites (RSGS) team prepare flight Robotic Arm System (RAS) #1 for thermal vacuum testing.
Credit: Sarah Peterson, U.S. Navy
What kind of test facilities let you simulate weightless robots on Earth?
Using our Gravity Offset Table, for instance, we can grapple sleds floating on air bearings to provide-high fidelity contact dynamics data. This data can then be correlated to models allowing us to simulate operating conditions in orbit. Using NRL’s thermal vacuum chamber, we can test the payload in thermal conditions it will see in space [from the deep frigidity of Earth’s shade to the punishing heat of direct sunlight] and ensure performance is understood in those conditions before we launch.
How is collision avoidance performed as the servicing vehicle closes in on the client satellite it needs to repair or refuel?
Our robotic payload incorporates algorithms that use relative pose data produced by the [RSGS] spacecraft, along with models of the servicing vehicle and the client spacecraft. This provides autonomous collision avoidance. Operators on the ground also actively monitor grapple operations in near-real time to provide additional layers of safety.
How does the servicer attach itself to the target satellite without fumbling and shedding space debris?
The robotic system has two types of grapple tool. The first was developed by NRL and is designed to grapple Marman rings — a type of launch vehicle interface found on many GEO spacecraft. The second, the POD Capture Tool, was developed by MDA [of Brampton, Ontario, developer of the Canadarm robots on the International Space Station] and is designed to capture a mating adapter called the POD Grapple Fixture, which can be mounted on any spacecraft RSGS services.
On Earth, in the realm of visual AI, computer-generated images are being generated en masse to train machine vision systems so all corner cases are covered. Is that the case here?
We don’t train our machine vision system, as it isn’t a machine learning-based algorithm. But we tested and verified our machine vision algorithms using real-world images under various lighting and thermal conditions in our machine vision lab. We use real-world images for system-level ground testing and dynamically generate synthetic imagery for closed-loop software testing.
Imagine an adversary nation wanted to damage or deorbit a NATO spacecraft with an orbital robotic asset. Could a servicer be hired and repurposed to defend against sabotage instead of just performing repairwork?
The RSGS program is a public-private partnership between DARPA and Northrop Grumman’s Space Logistics subsidiary. Space Logistics will own and operate the vehicle and make cooperative servicing available to both military and commercial GEO satellite owners on a fee-for-service basis.
Paul Marks is a technology journalist, writer, and editor based in London, U.K.
Join the Discussion (0)
Become a Member or Sign In to Post a Comment