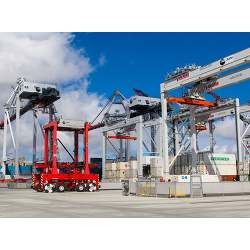
While there has been an outsized amount of hype around self-driving cars over the past few years, regulatory and technological challenges likely will delay their introduction until at least the early part of the next decade. In fact, it is more likely that types of autonomous vehicles that can be operated within an enclosed setting, such as vehicles used on construction sites, will gain traction before self-driving cars do.
San Francisco-based Built Robotics is taking the lessons learned from the industrial robotics market and applying them to construction vehicles, equipping them with technology that allows the vehicle to conduct work that is dangerous, repetitive, or both, with very little human intervention. In October 2017, the company launched its autonomous track loader (ATL), which can be used for digging out and grading a large, well-defined area, such as the foundation for a building.
Using a combination of LIDAR sensors, inertial measurement units (IMUs), and global positioning system (GPS) technology that allows for location-sensing down to the centimeter, the ATL can handle basic construction site tasks, such as digging foundation holes.
Unlike stationary automotive robots, which are usually programmed by moving the robot into position in a stepwise fashion, the ATL can work autonomously once it has been given specific parameters.
"We actually don't preprogram the machine; we just give it goal parameters, and all the path planning, progress monitoring, and decision making are completed autonomously," says Kelly Dillon, Built Robotics' head of People Operations. "We create a geofence for the job site and give the machine goal parameters," which include where to dig and where to place the dirt that has been excavated, and the vehicle will operate autonomously within those parameters.
Dillon notes the ATL and other autonomous construction vehicles are designed to address key issues impacting the construction industry, including a shortage of skilled labor, a desire to increase efficiency on the job site, and demand for enhanced worker safety.
"Our ATL can do the more dangerous or repetitive aspects of the job, enabling skilled operators to focus on the challenging tasks and letting contractors complete more work and get more done," Dillon says. She noted that while the ATL is particularly suited for handling relatively simple tasks, humans are still required to manage and complete more complex jobs, such as excavating around buried utility lines, fine grading of work sites, and loading trucks.
It's not just newcomers that are bringing autonomy to construction and other industrial settings. Caterpillar, one of the world's largest manufacturers of heavy equipment, has deployed more than 100 autonomous haul trucks to mines throughout the world. As of the fall of 2017, Cat's current autonomous fleet includes 56 Cat 793F trucks that have achieved 20% greater production than manned trucks working in the same mining complex. These trucks are also integrated with a fleet of more than 150 manned vehicles, including graders, loaders, water carts, light vehicles, and bulldozers, which are all managed via the Caterpillar MineStar System.
The benefits have been clear, with Cat noting that in less than five years of operation, the company's autonomous trucks have hauled 400-plus million metric tons of material with greater than 99.95% system availability, worked an average of 2.5 more hours per day compared with manned vehicles, and posted no human injuries.
Speaking at an investor meeting, Caterpillar Resource Industries group president Denise Johnson, said that "autonomy is no longer an experiment. We're seeing increasing pull from customers, and we're currently tracking 100-plus opportunities."
According to the company, Caterpillar has worked with Blacksburg, VA-based Torc Robotics for the past decade, with the latter company helping to develop Caterpillar's RemoteTask skid steer remote control system, introduced in 2015. More recently, Caterpillar has partnered with Torc to develop a system in which a Komatsu 930E haul truck can be operated by the Caterpillar autonomous haul truck system. This product is slated to be on the market by early 2019.
Regardless of the control system used to automate construction equipment, cybersecurity remains a key concern, given the potential damage that could be caused by heavy equipment that is under the control of malevolent actors.
"I think the biggest challenge to autonomy is going to be on the security side," says Bob Schena, chairman, CEO, and co-founder of Rajant Corp., a wireless mesh networking company that works with construction equipment manufacturers, transportation companies, and other industrial customers. "If governments and regulators believe that equipment could be hacked, taken over, and controlled by bad actors, they're not going to allow autonomy. So, this is an issue that will have to be addressed, and we're very involved in that."
Schena says the Rajant Kinetic Mesh technology, which was developed from military-grade applications, is designed to protect control and performance-metrics data from the network, both while the data is in transport and use, and when it is dormant, which serves as a further safeguard from potential hackers.
Indeed, protecting construction equipment from outside intrusions isn't just about stopping potential terrorists; some hackers may simply choose to attack weak networks for the thrill.
"Right now, we are working with construction companies that are going to use our solutions in order to securely connect their equipment," says Moshe Shlisel, CEO of GuardKnox, a Ramle, Israel-based company whose technology "protects the users of the connected vehicles against threats that can endanger their physical safety and the safety of their personal information," according to the company's website. Shlisel says many construction companies are using relatively weak connectivity software to actively monitor and control heavy equipment, such as cranes reaching nearly 200 feet tall.
"The manufacturer of the construction equipment would like to be able to monitor and to predict some malfunctions [by keeping an active and constant wireless connection to the crane], Shlisel says. "But you have to do that securely, otherwise you're having a connected motor or a connected crane that is exposed to every hacker that, just for fun, says to himself, 'well, let's see if I can control this crane remotely'."
Keith Kirkpatrick is principal of 4K Research & Consulting, LLC, based in Lynbrook, NY.
Join the Discussion (0)
Become a Member or Sign In to Post a Comment