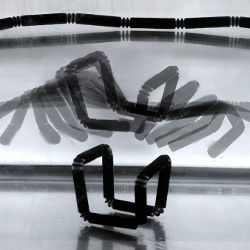
Imagine a pair of running shoes that grow spikes on their soles to gain traction when it starts to rain in the middle of a run, or camouflage material that changes color as the light changes. Those are just some of the applications that might become possible with a new technique known as 4D printing, developed by Stratasys Ltd., Autodesk, Inc., and Self-Assembly Lab at MIT.
The concept starts with additive manufacturing (3D printing), in which a machine builds a three-dimensional object by depositing successive layers of a material—polymers, resins, metals, ceramics—in almost any shape a designer can imagine. 3D printing has been garnering headlines and gaining a foothold in the world of manufacturing in recent years. The industry analysis firm Wohlers Associates says the worldwide market for 3D printing products and services reached $2.2 billion in 2012. Now some researchers are taking the next step by adding a fourth dimension—time.
“We want to be able to print objects, products, materials that transform over time,” says Skylar Tibbits, a research scientist who runs MIT’s Self-Assembly Lab in Cambridge, MA. “Why can’t we print dynamic things, or responsive things?”
The idea is to build an object out of multiple materials using a 3D printer. The materials would have different properties—their stiffness, say, or their sensitivity to temperature or moisture. For instance, one material might shrink a lot when heated, while another would not. By placing those different materials in the right configuration, a designer could determine what shape the object would take when heated.
The idea of materials that change their shape in response to some stimulus is not unique to 4D printing; other researchers have worked on “programmable matter,” such as thin sheets of solar cells that can unfold in response to a temperature change. Combining that idea with 3D printing, though, marries the usefulness of active materials to the new approaches to manufacturing provided by the printers.
For instance, being able to print something in one form and having it open up into another makes it possible to print objects that are larger than the 3D printers. Also, printing something in a compact form could involve less wasted material, and take less time, than printing it in its final shape. If an active object can be printed in a single piece, without having to screw in or glue on additional components, it should be cheaper and quicker to build and have fewer possible ways to break. “The more components you have, the more failureprone your system is,” Tibbits explains.
In one demonstration, Tibbits printed a black polymer into a flat disk. He then added to one side of the disk four concentric rings of a silver-colored polymer. Halfway between each pair of rings, but on the opposite side of the disk, he placed more rings of the same silvery polymer. When he immersed the disk in water, it bent along the rings, upward where the rings were on top and downward where they were on the bottom, in accordion-like pleats, forming a ridged, saddle-shaped object.
He also made a series of joined squares, with ridges where they intersect; when he wets that, it folds along the ridges into a cube.
Most of Tibbits’ work so far has focused on demonstrating that this process actually works, and figuring out ways in which to design responsive objects. He is not working on building any sort of commercial products, but says some may emerge in just a few years. One early application, he projects, will probably be sports apparel: a piece of clothing might react to an athlete’s body heat and open up pores to cool the athlete down, or close up if it sensed rain. Another use, he says, might be in infrastructure, such as water pipes that expand or contract to alter water pressure or flow rate.
While those kinds of applications would require that changes be repeatable and reversible, in other uses it would be enough to have a shape that changes only once. One notion that appeals to Carlos Olguin, head of the Bio/Nano/Programmable Matter Group at Autodesk Research in San Francisco, CA, is to create self-assembling furniture. A customer might purchase, say, a chair from a store and carry it home in a small, compact form. Once home, the customer would apply whatever stimulus the material was designed to respond to, and the clump would unfold into a chair that would then maintain its shape.
“4D printing in many ways is just another form of programming matter,” says Olguin, who collaborates with Tibbits. Olguin is working on developing the computer-aided design tools that will let engineers figure out where to place the material to get the function they are seeking. His work is part of Autodesk’s Project Cyborg, which is developing a CAD platform that uses computational resources in the cloud to provide modeling, simulation, and design optimization for material at different size scales.
Olguin’s hope is that a user working with traditional CAD software could design a desired object—a customized version of that chair, for instance—and that the computer could then apply a transformation algorithm to come up with the shape that, once printed, could become the chair. To do that, the system would need plenty of information about the characteristics of the materials the printer would use, and would have to arrange the materials in a way that would lead to the outcome the user intended. That is still a very tough problem, Olguin says. “It’s not just about software coding. It’s about getting materials to behave in the way that you want.”
“It’s not just about software coding. It’s about getting materials to behave in the way that you want.”
Tibbits would also like to be able to give a computer a description of the product he wanted—not only its shape, but its abilities—and have the machine figure out just which materials to use and where to place them. When he started this research a couple of years ago, most of what he did was empirical: building things and seeing how they worked. Since then, he has been building up more data about the properties of the materials he works with, which allows him to do more simulation before actually building a device. While he is investigating the 4D-friendly properties of existing polymers, he hopes materials scientists will also develop new materials with characteristics a 4D printer might be able to utilize.
All of Tibbits’ work so far has used water as the catalyst to make an object change shape. Jerry Qi, who studies the mechanics of materials at Georgia Institute of Technology in Atlanta, focuses on the fact that many polymers exhibit shape memory behavior with temperature changes. Heated above a certain point, the polymers become pliable enough to be bent into a shape, which it holds when it has cooled; heat it to the same temperature again, and it reverts to its original shape. The temperature at which the transition happens is different for each polymer.
Qi uses a 3D printer that heats and deposits polymer fibers. By controlling the diameter and orientation of the fiber, and how close to the surface he places it within another polymer, he can control how the fiber bends. “You have a lot of freedom,” he says. “You can control what kind of deformation you get.”
Depending on the material used and the design of the object, the temperature difference needed to induce a change can be fairly small. One potential use Qi sees is for a medical device such as a stent, which can be built in compact form for easy placement inside an artery; once in place, the body’s own heat would make it expand to fit.
So far, these researchers are working exclusively with polymers. Though it is possible to get some shape-changing behavior with a single material and clever design, it works better with multiple materials. The only 3D printers currently on the market that are capable of printing multiple materials come from Stratasys, and those print using only different types of polymer. Many researchers are working on ways to print more disparate materials together so that they could, for example, deposit metal wires inside ceramics, or build plastic parts with embedded circuitry. Because the processes for printing with different materials vary widely—the temperatures that melt metal to form parts also vaporize plastic, and inkjet printers that work nicely with one type of ink quickly clog with another—it could be a few years before more complex material designs are realized.
Being able to incorporate more capabilities, including electronics, in a 3D printed object could lead to devices with even greater abilities. “You could add sensing, maybe actuating capabilities, into your structure,” Qi says. One application might be used as the skin of an airplane or the heat-shielding tiles on a space shuttle; the material might be able to sense damage and alter its shape to self-heal, forming a temporary patch to protect the craft until it can be properly repaired.
Olguin argues that another area of research—3D bioprinting—might also be considered a form of 4D printing.
Olguin argues that another area of research—3D bioprinting—might also be considered a form of 4D printing. Researchers are trying to find ways to incorporate living cells into 3D printing, depositing them along with a soft matrix to form artificial organs or biorobots. In that case, Olguin says, the cells that grow and change over time bring in the fourth dimension.
The U.S. military believes 4D printing has potential. The U.S. Army Research Office last fall gave an $855,000 grant to a trio of researchers from the University of Pittsburgh, Harvard, and the University of Illinois to develop materials that would be useful to soldiers. Lead researcher Anne Balazs, a chemical engineer at Pittsburgh, says the group is concentrating on manipulating materials at a microscopic level to achieve desired properties, which might involve active camouflage or protection from shrapnel.
Though the field of 4D printing is still in its infancy, the researchers say it is likely to be only a few years before 3D printed objects that change over time start making their way into everyday use. “The momentum’s there,” Qi says. “This field is developing really fast.”
Further Reading
Ge, Q., Qi, H.J., Dunn, M.
Active Materials by Four-Dimensional Printing, Appl. Phys. Lett 103, 2013.
Tibbits, S.
4D Printing: Multi-Material Shape Change, Arch. Design 84 (1) 116-121 (2014)
Goldstein, S.C., Campbell, J.D., Mowry, T.C.
Programmable Matter, Computer 28 (6), 99-101 (2005)
Change Generation: Skylar Tibbits
http://vimeo.com/70660109
Figures
Figure. Above, a basic depiction of how a 3D printed object that changes shape or self-assembles over time becomes a 4D printed object. Below, one of Skylar Tibbits’ 4D objects; this 3D printed “self-folding straw” starts out as a cable-like structure, but it assembles itself into a pre-programmed shape when it encounters water.
Join the Discussion (0)
Become a Member or Sign In to Post a Comment