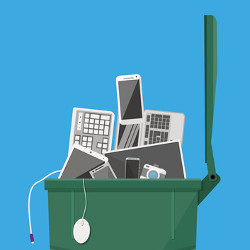
It is hard to imagine a world without electronic devices. From servers, personal computers, and storage devices to smartphones, tablets, and wearable devices, electronic devices drive businesses, entertain and enable consumers to interact with the world, and keep the world’s information and physical infrastructure networks running on a 24/7 basis. Not surprisingly, the number of electronic devices in use, particularly those that are connected to a network, continues to grow.
A 2019 Cisco VNI report forecast that on a global basis, there will be 28.5 billion networked devices in use by 2022, up from 18.0 billion in 2017, and 3.6 networked devices per capita by 2022, up from 2.4 per capita in 2017. Further, a December 2019 Deloitte study found that U.S. households own an average of 11 connected devices, including seven devices featuring screens on which to watch content, with expectations that the number of devices will increase further, overall and per person, thanks to the growth of new Internet of Things (IoT) products and applications.
While this is certainly good news for device manufacturers, content providers, and wireless service providers, there has also been enormous growth in electronic waste.
According to United Nations 2018 estimates (the most recent available), the e-waste stream has reached 50 million metric tons annually on a global basis. Managing this waste appropriately is of considerable concern; throwing electronic equipment, often containing extremely harmful chemicals and elements, into landfills or shipping them off to other countries, is simply no longer an option, due to both environmental concerns and geo-political issues, given that some countries are now refusing to process the waste they have accepted in the past from foreign nations.
Figure. When electronic devices reach end of life, internal components must either be recaptured for reuse or disposed of in ways that do not harm the environment.
The management of e-waste can be accomplished in a variety of ways, but at the heart of the process is the separation of materials. E-waste materials are physically shredded to facilitate easier sorting and separation of plastics from metals and components. Magnets are then used to separate ferrous metals from other elements, and these iron and steel fragments can then be resold as recycled steel.
Hydrometallurgical processes are used to separate metals; e-waste items such as printed circuit boards are dissolved into leaching solutions consisting of sulfuric acid, hydrochloric acid, nitric acid, aqua regia, and alkalis. The desired metals can then be recovered via a number of processes, including electrorefining, precipitation, cementation, absorption, ion exchange, and solvent extraction.
Meanwhile, pyrometallurgical processes including incineration, smelting in a furnace, dressing, sintering, and melting at high temperatures are used to burn electronic scrap waste, resulting in plastic being separated from the other components, while the metal oxides form a slag from which non-ferrous and precious metals can be recovered. An less-common technique uses bio-metallurgical processing, which leverages the physical-chemical interaction that occurs when metals are exposed to microorganisms such as algae, bacteria, and yeasts; when added to a solution containing the e-waste, these reactants can accumulate heavy and precious metals. Water separation technology can be used to separate the remaining waste stream, which is usually mostly plastic and glass.
While these processes certainly are effective, they can be expensive, in terms of the actual economic cost paid to separators, as well as the ecological cost of expending additional energy to carry out each process. At the current device recycling rate of 12%, according to the U.S. Environmental Protection Agency, the economic benefit of capturing and stripping out materials as a primary recycling strategy may be limited.
That’s why there is a growing interested in reducing the amount of hazardous or hard-to-recycle material at the point of design and manufacture, including hazardous chemicals, rare earth materials, or composite plastics that cannot be easily separated and recycled. Significant progress has already been made via the “lightweighting” of televisions, as manufacturers have shifted from the production of cathode ray tubes (CRTs) to flat-panel (plasma, LCD, and LED) displays, resulting in a smaller amount of plastic per television set, plus a reduction in the use of other harmful chemicals (such as lead, cadmium, barium, and a number of fluorescent powders).
However, the shift to smaller and lighter electronics is not all good news.
“Over time, the waste stream in the United States has actually gotten lighter [in terms of weight],” says Callie Babbitt, an associate professor in the Department of Sustainability at the Golisano Institute for Sustainability at Rochester Institute of Technology. “But that doesn’t mean it’s getting easier to manage, because the waste stream is more complex,” Babbitt says.
Indeed, in many devices, such as smartphones, tablets, and even wearable devices, more tightly integrated components are harder to separate, Babbit says, and the devices themselves are often sealed so even removing a battery can be a time-consuming challenge, making end-of-life recycling efforts both tedious and expensive. Further, as devices get smaller, the material value of electronic devices is getting smaller, requiring a greater number of devices to be recycled to capture the same amount of precious metals that can be resold.
Special attention also is being paid to reusing materials (such as plastics, metals, or composites) that can easily be separated and broken down by waste processors. Some manufacturers even design components that can be saved and recycled directly, without needing to be broken down to their core materials.
“Some companies are thinking more about the product design as a whole, making the product more easily reused or upgraded,” Babbitt says, noting that manufacturers increasingly think about substituting rare materials with more commonly sourced ones, reducing the number of different types of plastics used in composites, and eliminating compound materials such as resins or films adhered to plastics.
Further, China’s enactment in January 2018 of its National Sword policy has had major implications in the e-waste world. The country, which once accepted nearly 50% of the world’s recyclable waste, banned the import of most plastics and other materials into China’s recycling processors, forcing a shift from simply improving recycling rates to addressing the issue of e-waste before a product is even manufactured.
Designing products with consideration of the ease of recycling is a key element of the Electronic Product Environmental Assessment Tool (EPEAT), a program of the non-profit Green Electronics Council (GEC) that provides labeling for electronic products that meet certain criteria across a range of 12 categories, covering material and chemical usage, energy efficiency, recyclability, product lifespan, and product design. The EPEAT program is voluntary, and incorporates input from manufacturers; it can be thought of as a benchmark that can be utilized in a global market where environmental and recycling laws and regulations vary widely.
Explains Patty Dillon, director of criteria development for the EPEAT program, “When we have these required and optional criteria, it’s [designed] to get the market to move in that direction where [a goal] might not be immediately achievable, but it is something that can be achieved in a one- to two-year time frame.” Dillon says EPEAT often sets the levels for percentage of recycled content, energy efficiency, and product longevity, at easily achievable benchmarks to entice a wide range of manufacturers to join the program, and plans to increase these standards over time.
“Over time, the waste stream in the United States has actually gotten lighter, but that doesn’t mean it’s getting easier to manage, because the waste stream is more complex.”
“For example, the initial computer standard had no requirement except that [manufacturers] declare how much recycled content was included,” Dillon says. “There was no minimum level, but manufacturers could receive an optional point for 10% recycled content, while 25% recycled content got you two points. After a few years, we were able to go in and say, ‘Oh, look at where the market is’; now we have a 2% required recycled content level, because we know you can do it.”
EPEAT offers three levels of compliance to which manufacturers can design their products: Gold-rated products must meet all of the required criteria and at least 75% of the optional criteria; Silver-rated products must meet all of the required criteria and at least 50% of the optional criteria; and Bronze-rated products must meet all of the required criteria in their category.
Examples of required criteria vary by product category, but within the TV category, there are three required criteria: compliance with provisions of European Union (EU) Restriction of Hazardous Substances (RoHS) Directive; reporting on the amount of mercury in light sources; and compliance with the provisions of the EU Battery Directive. Meanwhile, there are 12 optional criteria, which are designed to push the industry forward in terms of reducing the use of certain substances, or eliminating specific materials altogether, such as using only non-mercury-containing light sources, or eliminating or reducing products’ flame-retardant material content.
The goal behind the labeling is to make both large and consumer purchasers of electronics more cognizant of the financial and environmental benefits of “greener” electronic design, as well as encouraging manufacturers to continually improve their product designs with regard to the issue of e-waste.
One of the primary components likely to become a concern over the next several years is the battery, used in many electronic devices today, but which may become even more prevalent as electric vehicles become more commonplace over the next decade.
Launched last year, the ReCell Center is a national collaboration of Argonne National Laboratory, the National Renewable Energy Lab, Oak Ridge National Laboratory, Michigan Technological University, the University of California at San Diego, Worcester Polytechnic Institute, and battery industry participants, that is funded by a three-year, $15-million U.S. Department of Energy grant. ReCell’s primary goal is to bring industry participants and researchers together to advance battery recycling technologies that can actually be used in a real-world commercial environment.
ReCell is focused on a few key areas related to battery technology, including identifying and developing materials that can be easily and cheaply recycled; developing direct cathode recycling (a process involving the retrieval of cathode materials from spent lithium batteries, and then regenerating the cathode materials by adding additional lithium into the structure of cathode material to create new battery-grade material) to eliminate the need for expensive hydrometallurgical and pyrometallurgical processes to recover specific battery metals; developing processes for recovering other battery materials; and using modeling and analysis to determine the best materials and chemistries for current and future batteries.
“The goal behind ReCell is to make battery recycling economically attractive,” says Jeff Spangenberger, the organization’s director. “At the national lab level, we create a lot of really cool technology, but we need industry [partners] to commercialize these technologies. We had as many industrial stakeholders as we could to come and meet with us to make sure that what we were doing made sense, and to help direct the work that we do. If nobody’s ever to commercialize the technology because they know it will never work in the business world, there’s no sense in us doing it.”
“Our goal is to make environmentally sound, economically attractive, recycling for lithium-ion batteries. No matter how is happens, it’s a win.”
Though ReCell is primarily focused on lithium batteries used in electric vehicles, Spangenberger notes that batteries used in consumer products may also benefit from ReCell’s efforts, noting that many electronic devices, such as smartphones, are designed so that it’s extremely difficult to even remove the battery, driving up the labor cost to recycle the battery technology. Any gains that can be made by ReCell’s efforts in the EV battery space likely will show benefits in the adjacent market of consumer devices, which also rely heavily on Li-ion battery technology.
“I think that it will be, and hopefully some of these technologies will transition into other areas of recycling,” Spangenberger says. “Hopefully they will gain some advantages from what we’re doing. Remember, our goal is to make environmentally sound, economically attractive, recycling for lithium-ion batteries. No matter how it happens, it’s a win.”
World Economic Forum, A New Circular Vision for Electronics Time for a Global Reboot, http://bit.ly/2ToM0l9
Cisco Annual Internet Report, VNI Forecast Tool (Device Forecasts), http://bit.ly/2Py5RgE
EPEAT Criteria, Green Electronics Council, https://greenelectronicscouncil.org/epeat-criteria/
Status of electronic waste recycling techniques: a review, Environmental Science and Pollution Research 25(4), May 2018, http://bit.ly/2PzBpmm
Join the Discussion (0)
Become a Member or Sign In to Post a Comment