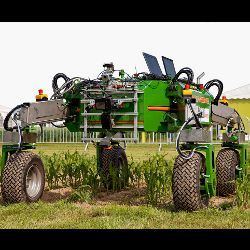
Field farming is “the world’s oldest profession,” and not just because food plants have been cultivated for over 10,000 years. Its individual practitioners are old as well, the median age rising rapidly as young people abandon the farming lifestyle (the U.S. Department of Agriculture reports a median age of 58 in 2012, up from 55 in 2002, with other countries showing similar data). Those who remain face the same repetitive work of seeding, weeding, feeding, and harvesting, the tedium of each task increasing as farms grow ever larger.
However, today’s agricultural robots excel at repetitive tasks, letting farmers tend to more strategic matters.
“When we develop robots, people always say they should increase yields or lower costs, but that’s not always the case,” says Eldert van Henten, a professor in Wageningen University’s Farm Technology Group. “Robots that offer the farmer time to devote attention to business and management also have economic value.”
Allen Lash, CEO of the farm management company Family Farms Group, sees agricultural robots filling in for the shrinking agricultural workforce. “In a lot of our small, rural communities, we just don’t have adequate labor to run big, sophisticated equipment anymore,” he says. “With autonomous equipment, you’ll need less labor, although the people you have will need more computer technology skills. They’ll control equipment remotely to a great extent, from a control room, scanning at least three cameras all the time. So we’ll get more acres covered in a more efficient way; maybe several thousand acres per employee, instead of today’s 1,000.”
Proponents believe robotic agriculture also will help ensure food is available for everyone, everywhere, from local sources. “Every country is now worried about food security, and the country next door has cheaper labor” said Salah Sukkarieh, director of Research and Innovation at the Australian Centre for Field Robotics (ACFR) at the University of Sydney.
Food security is one of the driving forces behind “The Vegetable Factory,” an indoor farm that the Japan-based company SPREAD Co. Inc. plans to open in Kyoto next year. In addition to computer-controlled lighting, temperature, and humidity, virtually every aspect of a plant’s development from seedling to harvest will be automated. “We expect automation to reduce human error, therefore stabilizing the quality and quantity of production,” says SPREAD global marketing manager J.J. Price. “Such ‘plant factories’ will increase in the future to cover agricultural issues, food shortages, and environmental problems.”
Command and Control
Farm automation is particularly difficult because the environment varies so much—especially when compared to clean labs. “Computer scientists need to get outdoors more,” said ACFR’s Sukkarieh. “A lot of the [computer vision] algorithms get developed on very structured data, like a camera focusing on objects in a kitchen. But in the field, the wind blows leaves around, lighting conditions change, you get a bit of dust; these all affect the algorithm. We try things out in the lab, but then have to play with them because they don’t work as well outdoors, in an unstructured environment.”
Traditional farm equipment also adds unpredictability to the mix, as Autonomous Tractor Corporation (ATC) president and CEO Kraig Schulz learned when his company started planning to build an autonomous tractor. “Traditional [drive train] vendors couldn’t deliver what we needed, so we turned to electric drive trains, like Google and Tesla have for their cars. A traditional drive train is hard to control; there’s a lot of mechanical nonsense between the driver and the ground. But I can control an electric motor to milliseconds and fractions of an inch.” The company later released its “eDrive” system as an electric engine replacement for tractors already in the field.
As another step toward autonomous farming, ATC next supplemented traditional GPS navigation with a local laser-and-radio system named AutoDrive. “If you talk to farmers, they’ll say that GPS is good, but far from perfect. They’re in very rural areas, where reception isn’t great, and GPS tends to suffer from problems like sunspots, reflections, and tree coverage,” says Schulz. “A lot of driverless cars use optics and radar and such, because there’s stuff around them to see. When you’re in a field, there’s nothing to see! So you need a second or third source of data to get relative positioning in the field.” The company is now working on a system that can be retrofit to any tractor with its eDrive, adding AutoDrive and its own “FieldSmart” artificial intelligence software.
An “App” for Planting
Another challenge for autonomous farming is the variety of tasks that agriculture demands. The hardest, according to Wageningen University’s van Henten, is selective harvesting. “Robots can do the trick now at relatively slow speeds, and without full success,” he says. “We still have a long way to go. But humans excel in terms of eye-hand coordination, intelligence, flexibility, and robustness against variation in the environment. So harvesting is done by humans very effectively.”
One problem, he says, is that “Plants that are members of the same type can differ a lot due to a lack of water, light, or nutrition.” Switching from one variety to another is also difficult. “Consider the tomato; usually a tomato is red, but there are some that are yellow. There are also different shapes, and beefsteak and cherry tomatoes have very different sizes. But the robot still has to recognize them as tomatoes.”
A somewhat simpler task is weeding, which is the bailiwick of the French company Naïo Technologies. “We started with weeding because it’s very arduous for farmers,” says Julien Laffont, the company’s international business developer, “and it’s a repetitive task, so it’s perfect for robots.” The company’s currently available “Oz” system uses two cameras and a laser to guide itself between rows of crops as it drags a weeding tool behind it.
Oz controls only the robot, not the tool it drags behind. Laffont said the company’s future “Dino” robot also will control the tools themselves, letting them do more than simply avoid harming crops. “We’ll use cameras that analyze the image to detect, circle, and count crops. We might also have applications to analyze the images for things like disease.”
A different approach to weeding can be found in “Lettucebot,” a product from U.S.-based Blue River Technology that puts its intelligence in the implement, combining vision technology with microspraying to apply herbicides to weeds and overplanted lettuce sprouts. According to the company, Lettucebot can identify 1.5 million plants per hour, weeding and thinning a 40-acre field within a day. For vice president of business development Ben Chostner, speed is only one benefit to this precision approach. “Most inputs or chemicals on the farm are applied in a broadcast way, with hardly any sensors. It’s like if someone in San Francisco had an infection, and the only solution was to give everyone an antibiotic; that would solve the problem, but it would be very expensive and inefficient, and would lead to negative consequences like resistance. That’s the same thing that’s happening with weed control today, because those are the tools we have.”
ATC’s Schulz looks forward to the day that weeding, planting, and harvesting are all treated as “apps” that a single machine (with specialized attachments) could learn to perform through artificial intelligence (AI) techniques. “The computer has to become a farmer just like a person becomes a farmer, over time, by learning. That’s where AI comes in. The driver should think of the tractor riding along like a son or daughter: it observes what the farmer is doing and thinks, ‘this is what I have to replicate.’ The tractor will start with small tasks and grow competence over time. Its tillage ‘app’ is very different from a planting ‘app’ because the task has fundamentally different controls, but the learning process could be similar.”
From Automation to Automatons
Kubota Corp. director and senior managing executive officer Satoshi Iida differentiates modern, computer-driven agents from centuries-old farming technology like the seed drill. “An agricultural machine can be defined as a ‘robot’ when it has the three technology components,” says Iida, who also is general manager of Kubota’s Research and Development (R&D) headquarters, and of the company’s Water and Environment R&D function. “It must have sensors that perceive its own situation; intelligence and control mechanism for determining and selecting the appropriate action by itself; and driving mechanisms for achieving what it has determined.”
Blue River Technology’s Chostner says, “A robot sees, decides, and acts. Then it closes that loop by seeing how it acted and adjusting its future actions.” On the other hand, Chostner says, “We’d much rather focus on the simplest tool that will create value for our customers, rather than the ultimate ‘robot’ that is the company vision. Robots are always something out in the future; automation is something that’s here today, creating value. We found that farmers don’t like to buy robots; they like to buy machines that work.”
Except for limited tasks by “machines that work,” fully automated growing may be years away. Kubota’s Iida believes the technology is now in the second of four stages: we have achieved automation of individual functions and auto-steering under operator control, but have yet to master unguided operation and fully autonomous farming.
Sukkarieh believes economic changes have cleared the way to reach that final phase. “Farming is probably the last major primary industry to focus on automation, and that’s because of the cost,” he says, “but technology costs have dropped dramatically. Even places with cheaper labor are considering agricultural automation. I think over the next year or two, you’ll see a large amount of activity happening in this space.”
Robotics & Automation Society, Technical Committee on Agricultural Robotics and Automation, IEEE: http://www.fieldrobot.com/ieeeras/
Past IEEE webinars on agricultural robotics: http://www.fieldrobot.com/ieeeras/Events.html
Video of Lettucebot: https://www.youtube.com/watch?v=yCPe9Sy0TFY
Robohub focus on agricultural robotics: http://robohub.org/tag/robohub-focus-on-agricultural-robotics/
Australian Centre for Field Robotics (Agriculture Projects): http://sydney.edu.au/acfr/agriculture
Join the Discussion (0)
Become a Member or Sign In to Post a Comment