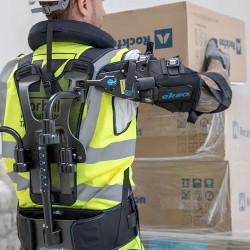
Millions of people Suffer from the effects of spinal cord injuries and strokes that have left them paralyzed. Millions more suffer from back pain, which makes movement painful. Exoskeletons are helping the paralyzed to walk again, enabling soldiers to carry heavy loads, and workers to lift heavy objects with greater ease.
An exoskeleton is a mechanical device or soft material worn by a patient/operator, whose structure mirrors the skeletal structure of the operator’s limbs (joints, muscles, etc.). The structure works in tandem with the person wearing it, and it is utilized to amplify their capabilities, serving as an assistive device, haptic controller, or for rehabilitation purposes, says Rian Whitton, an analyst at technology market intelligence firm ABI Research. The firm is forecasting 150,618 exoskeleton shipments in 2028 and $2.9 billion in revenue in 2028, up from $104 million in 2018.
The technology has been around since the 1960s; during the Cold War, however, the focus was mainly on research and exploration, Whitton says. Research and development activity picked up again in 2017, he says, when exoskeletons began to gain regulatory approval and were popularized in the health market.
“You have this increased market due to the number of veterans with spinal cord injuries resulting from conflicts post-9/11, and the prosthetics market and robotic limbs market was accelerated because of that now,” Whitton says. “So you could argue the military … had a stimulating effect.”
That said, exoskeletons are still in a “very nascent state,” Whitton adds.
Hermano Krebs, the self-described “father of rehabilitative robotics” and principal research scientist in the Mechanical Engineering Department of the Massachusetts Institute of Technology (MIT), agrees. Until the 1970s and 1980s, he recalls, the perception was that the brain was hardwired, and there was not much that could be done for a person who suffered a stroke. Today, the concept of neuroplasticity, the brain’s ability to form new neural connections, has shown that a person’s brain functioning can grow stronger after suffering a stroke, says Krebs.
Figure. A Ford worker wearing the EksoVest, which provides lift assistance for repetitive overhead tasks.
When Krebs began his research, his goal was to “create tools to help a clinician take advantage of the nurture that we could offer over the nature.”
Applying robotics using concepts from neuroscience is helping people recover what they lost, he says. “It’s not a cure, but it improves care … This is the direction of rehabilitative technology.”
There are different types of robotics. In one scenario, a robot might be mounted on a wheelchair and feed a person by bringing a spoon to their face, which is an assistive application. Alternatively, an exoskeleton robot could be mounted around the person’s arm to help them bring the spoon to their own face.
“Both have value, and it depends on what the application is,” Krebs says. “Now you can think of [exoskeletons] … not just in rehabilitative medicine, but in the aging of the population or for workers in factories, depending on what the goal is.”
Krebs and a team at MIT created a plastic exoskeleton known as Anklebot during 2003–2004. Anklebot is mounted around a person’s ankle to help them after a stroke, since many stroke victims cannot lift their ankles to clear the floor when walking, he says. The Anklebot is designed to help the person propel him/herself forward and clear the floor by lifting the ankles so they don’t fall.
Today, Krebs says, many U.S.-based companies have commercialized the Anklebot to treat patients, while several others have developed their own technologies for helping post-stroke patients lift their ankles. One is Japanese-based Yaskawa, which also has an ankle robot to help stroke patients. Krebs also started a new company called 4Motion Robotics, which will be designing an anklebot and other exoskeletal products.
Increased use of exoskeletons is also being driven by re-shoring, the bringing back of manufacturing jobs to the U.S. from offshore, notes Whitton. Exoskeletons can be beneficial in helping workers avoid injuries and stay on the job longer because they “amplify human performance,” which results in a productivity gain.
“There is an acute labor shortage in industrial jobs here; there is a low participation rate and a lot of people are feeling the pinch and [companies are] struggling to grow and raise productivity due to a lack of workers and also an aging workforce.” Already, people are retiring later, he noted, “so in a sense, this is a way of extending human life and extending their time in the labor force.”
Couple those factors with injuries on construction sites and mining operations, and you can understand why exoskeletons are being eyed as a way to extend the life of the worker, because they can amplify performance.
Take, for example, a Milwaukee Grinder, a power tool mainly used to grind metal in discrete manufacturing, and a piece of equipment that can weigh 15 lbs. or more, Whitton says. An exoskeleton with a third zero-gravity arm could pick it up without requiring any exertion on the part of a worker, he says.
That appeals to home improvement chain Lowe’s, which tested exosuits in April 2017 at its Christiansburg, VA, location, in partnership with Virginia Polytechnic Institute and State University (Virginia Tech). “We gathered feedback from the test and are now using the data to help define the next phase of the program,” says a Lowe’s spokesman, who declined to provide further details.
Ford Motor Co. is also testing at one of its assembly plants a wearable exoskeleton called EksoVest to help reduce shoulder injury, which is an issue in assembly line work.
The flip side of exoskeletons, however, is that it could take a while for a company to recoup its initial investment because they are extremely expensive right now, notes Whitton. An upper-body exoskeleton designed to amplify human performance runs about $30,000, he says, “but the price is coming down, and eventually these technologies will be commoditized.” Additionally, he anticipates the cost of an exoskeleton will shift from hardware to software and robotics as a service with a monthly subscription model; this, he believes, will lower the barrier to adoption.
Exoskeletons can be beneficial in helping workers avoid injuries and stay on the job longer because they “amplify human performance,” which results in a productivity gain.
Jerryll Noorden, a Connecticut-based real estate investor, is also bullish on exoskeletons. Prior to real estate, Noorden was the mechanical lead engineer on the National Aeronautics and Space Administration (NASA) X1 Exoskeleton, as well as working at the Florida Institute for Human & Machine Cognition (IMHC), a research institution of the State University System of Florida. Noorden believes so much in the viability of exoskeletons that he says he is planning to donate some of the proceeds from his business to exoskeleton research and development.
While working at IHMC in 2007, Noorden and others developed a prototype for an exoskeleton, which he says was “not very successful” because a motor was required for each joint to introduce movement. “The stronger the motor, the bigger it has to be, and that is the huge issue with motors right now,” Noorden explains. “The more power, the bigger the motor, and of course, it becomes heavier.”
The IHMC team came up with a second prototype, called Mina, in the 2008–2009 timeframe, which was much more successful, according to Noorden. At that point, he was contracted by IHMC to NASA, which he says was interested in the technology to help astronauts exercise in space.
However, after dealing with the fallout of budget cuts at NASA, Noorden decided to go out on his own and start a real estate investing business, “so that I could continue doing research without having to ask the government for funding.”
In the meantime, several things need to happen for exoskeletons to improve, observers say. Like Noorden, Krebs says, “We’re still not only trying to hide the hardware, but make it lighter. Many of the actuators and motors are still bulky, and it’s not easy to reduce the weight of the devices.” If the weight is reduced, “many times we don’t have the behavior we need,” meaning when the motor becomes smaller, it becomes more difficult for a person to move. “Ultimately, you want to devise something transparent that will help move you and assist you but won’t hold you back. But we’re not there yet.”
Not only is the goal to make a exoskeleton device lighter, but also for it to behave in a way that people feel good about it, so it does not hold them back or prevent them from doing a particular movement. “This balance is what makes engineering difficult,” Krebs says.
Yet, Krebs believes within 10 years the technology will have come far enough that it will be “far more available in multiple settings.”
He also thinks exoskeletons will be front and center at the Tokyo Summer Olympics games in 2020. Toyota’s Partner Robot division has developed a device to exercise the knee of a patient, and many other Japanese-based companies also are working on exoskeleton rehabilitation devices, he says. “I think the [Tokyo] Paralympics will be more interesting than the regular Olympics,” he says, “because there will be lots of demonstrations of technology to help people move,” due to the number of Japanese companies that are working on exoskeletal technology now.
“Ultimately, you want to devise something transparent that will help move you and assist you but won’t hold you back. But we’re not there yet.”
In healthcare, the main goal is to make exoskeletal devices “essentially disappear” and become “soft exoskeletals.” Many people are working right now on incorporating such systems into clothing, Krebs says, such as a pair of pants with wires or cables that would be able to assist a person’s mobility. One is an Israeli company called ReWalk Robotics, which has partnered with The Wyss Institute at Harvard University to make assistive exosuits devices for people with lower-limb disabilities.
Whitton thinks that as a result of the cost and “complexity of the health supply chain,” due to a strict regulatory environment and the need to tailor an exoskeleton to an individual, healthcare will not be the biggest market for exoskeletons. He anticipates greater adoption in industries like manufacturing, mining, and defense.
“In many cases, a robot isn’t sufficiently adaptable or dexterous to perform a wide number of tasks,” Whitton explains, whereas industrial and mobile robots and exoskeletons are aimed at assisting human workers to enable them to do more, and more easily.
Whitton also foresees the systems becoming lighter and more dexterous and expects them to be deployed like Internet of Things (IoT) devices with artificial intelligence (AI) capabilities such as data analytics, to monitor worker performance and measure when a worker might be most at risk for injury. Exoskeletons are going to be laden with sensors and will be connected with other wearables like mobile control panels, he says. “While current systems are somewhat rudimentary, the aim is to track historical data about worker body positioning and to track [an] exosuit’s location through the workspace.”
Significant progress needs to be made on the social side, too. “There needs to be a greater sense of their transformative potential and the potential to get sufficient ROI in a sufficient amount of time,” Whitton adds. Exoskeletons are “a capital-intensive technology and we don’t know when the ROI will be. I think that will change over time as they are deployed by bigger companies.”
Rupal, B.S., Rafique, S., Singla, A., Singla, E., Isaksson, M., and Virk, G.S.
Lower-limb exoskeletons: Research trends and regulatory guidelines in medical and non-medical applications, International Journal of Advanced Robotic Systems, 2017.
Luo, J., Pan, B., and Fu, Y.
Experiment research of human lower extremity exoskeleton robot, Proceedings of the 32nd Chinese Control Conference, 2013 https://ieeexplore.ieee.org/document/6640490/authors#authors
Baldovino, R., and Jamisola, R.
A Study on the State of Powered-Exoskeleton Design for Lower Extremities, 5th International Conference on Humanoid, Nanotechnology, Information Technology, Communication and Control, Environment, and Management 2009 (HNICEM 2009) http://bit.ly/2HhaWIl
Neuhaus, P.D., Noorden, J.H., Craig, T.J., Torres, T., Kirschbaum, J., and Pratt, J.E.
Design and Evaluation of Mina a Robotic Orthosis for Paraplegics, Proceedings of the 2011 International Conference on Rehabilitation Robotics (ICORR 2011), Zurich, Switzerland http://bit.ly/2Ct9E7H
Kwa, H.K., Noorden, J.H., Missel, M., Craig, T., Pratt, J.E., and Neuhaus, P.D.
Development of the IHMC Mobility Assist Exoskeleton, Proceedings of the 2009 IEEE International Conference on Robotics and Automation, (ICRA ’09), Kobe, Japan http://bit.ly/2Fzn2uJ
Gui, L., Yang, Z., Yang, X, Gu, W., and Zhang, Y.
Design and Control Technique Research of Exoskeleton Suit, IEEE International Conference on Automation and Logistics, 2007 https://ieeexplore.ieee.org/document/4338624/authors#authors
Join the Discussion (0)
Become a Member or Sign In to Post a Comment