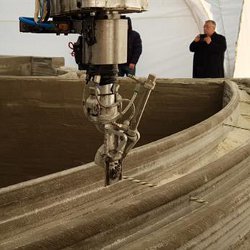
The construction of New York’s Empire State Building is often seen as the figurative and literal pinnacle of construction efficiency, rising 1,250 feet and 102 stories from the ground to its rooftop spire in just over 13 months’ time, at a human cost of just five lives. Indeed, most of today’s construction projects would be lucky to come close to that level of speed, regardless of the building’s size. While the construction industry traditionally has been slow to change the way it operates, several new technologies are poised to usher in a new era of faster and more automated construction practices.
Three-dimensional (3D) printing is among the key technologies that are expected to change the way structures are built in the future, as construction engineers and contractors seek methods for completing buildings more quickly, more efficiently, and, in many cases, with a greater attention paid to sustainability. Large printers that can print construction materials such as foam or concrete into specific shapes can drastically speed up the creation of walls, decorative or ornamental pieces, and even certain structural elements. Furthermore, in some scenarios, custom-built or unique items can be created onsite or in a factory, at a much lower cost than by using traditional, one-off casting techniques.
“If you can focus on [printing] the more labor-intensive components of the structure, then the productivity will increase,” says Pelin Gultekin-Bicer, Building Information Modeling (BIM)/Virtual Design and Construction (VDC) project manager at VIATechnik LLC, a construction and engineering services firm based in Chicago. In addition, she says, “if you can integrate the 3D printers onsite, then you can improve the productivity, as [the construction schedule] will be more predictable.”
Figure. A concrete villa in Binzhou, China, that was produced by a 150-meter-tall 3D printer.
The most common commercial use of 3D printing today is to create the molds that are used to cast concrete panels for use in a building or tunnel, which is how the technology is being used by Australia’s Laing O’Rourke, a multinational construction company. Laing O’Rourke’s FreeFAB technology employs employs a 100x25x15-foot robotic 3D printer that prints molds measuring 6×4.5 feet from a specially designed wax. These molds are used to cast large concrete panels at an offsite factory that are unique, in terms of size or shape, and likely would require a large traditional wood or polystyrene mold to be created for each panel.
According to the company, the FreeFAB technology is more eco-friendly and efficient than creating conventional wood or polystyrene molds, because it can print to an exact shape with micron-level accuracy, and the wax molds can be melted down for reuse again and again.
The completed panels are shipped and installed into the passenger tunnels of London’s Crossrail railway construction project. Crossrail will be a high-frequency, high-capacity railway serving London and the Southeast U.K. According to James Gardiner, CTO and cofounder of FreeFAB, a spinout of Laing O’Rourke, utilizing 3D printing to create the molds, rather than the panels themselves, incorporates all of the benefits (speed and quick customization) of 3D printing, while minimizing the technology’s weaknesses.
Gardiner notes that 3D concrete printers require very specific temperature and humidity levels in order for concrete to set properly. In addition, if a 3D printer pauses or stops, the homogeneity of each layer of concrete, and the bonds between each layer, will be compromised. This introduces questions about whether the material and building process will be able to be certified by local building authorities, given that any material used in construction must meet load-handling, weatherproofing, and other specific building code issues.
“[Research universities] are starting to focus on the characterization of 3D materials, trying to develop specific materials that are particularly well-suited for 3D printing and understanding those already used,” Gardiner says. “But I’d say that it’s still got a little way to go.”
Other organizations, however, have taken to using 3D printing to construct entire buildings. Chinese company WinSun claims that in 2008, it printed an entire house using 3D printing technology in just two days. The company has since 3D-printed larger structures, such as a five-story section of a city block, as well as one of its own manufacturing plants in Suzhou Industrial Park. Each of these projects took about a month, far less time than would be required with traditional construction techniques.
According to industry professionals, however, WinSun’s 3D-printed building technology still requires that the individual walls, floors, and roof be fastened together using traditional methods, including bolting walls and roofs together, and much of the internal elements of a house (ductwork, electrical conduit, plumbing, and other finishes) must still be installed, rather than printed.
“They’re not printing an entire six-story apartment building in one go,” explains Casey Mahon, digital practice manager at Carrier Johnson, an architectural, interior design, and branding practice based in San Diego, CA. “They’re printing it in pieces. Those pieces are coming out to the job site, and they’re getting assembled. Then they’re getting clad with some tile or stone on the exterior. It’s rare that you ever see an interior photograph of one of those projects. When you do, you can see that, it’s clear, all the conduit is surface-run, all the fixtures are surface-mounted fixtures.”
Meanwhile, researchers in France from the University of Nantes, Nantes Métropole, Nantes Métropole Habitat (NMH), and Ouest Valorisation, with help from teams at the Nantes Digital Science Laboratory and the Institute of Research in Civil and Mechanical Engineering, are working to create an industrial 3D printer that will be able to build a demonstration house in only a few days. Called BatiPrint3D, the printer was completed in the fall of 2017. The device prints the home in three layers, including two foam layers for insulation, and a third concrete layer. Of course, the technology is simply being demonstrated, and is not yet ready for mass commercialization.
Similar to the WinSun house, a real functioning house would need to have its infrastructure and finishes added after printing, thereby putting real construction times in line with those of traditionally built houses.
That is why it is most likely that 3D printing will be primarily used either offsite, to facilitate the faster creation of molds to create one-off castings of unique panels or parts, or will be deployed onsite to print unique or bespoke architectural or decorative pieces of a structure, rather than entire houses, in the near future. By addressing the labor-intensive pieces via onsite printing, 3D printing likely will improve the predictability of scheduling of material delivery and improve worker productivity, which together are responsible for much of the costs related to construction.
“The biggest problem of the construction industry is the variance in schedule and cost estimation,” says Gultekin-Bicer, explaining that these include material costs, shipping costs, and labor costs. “Cost estimations are derived from the schedule, so if you extend the schedule of the building, you are also extending the cost,” she says, noting that the variability in the schedule is largely due to the human labor factor. “If you can integrate the 3D printers onsite, then we can improve the productivity, as [the schedule] will be more predictable.”
A bricklaying robot called SAM100 can lay 3,000 bricks a day, six times as many as a typical human bricklayer.
In the future, Gardiner notes, 3D printing will allow for a more streamlined use of materials, thanks to the ability to print both structural and decorative pieces of a building that place material only where needed for maximum strength, energy efficiency, or form, or to help them fit into unusual or tight site constraints.
“At the moment, if you build a concrete wall or a brick wall, you’re putting the same bulk material uniformly, regardless of where the stresses are on that particular element,” Gardiner says, observing that 3D printing will allow architects to design building components that put material only where they are absolutely needed, rather than simply adhering to a mass-produced shape.
It is not just 3D printing that is poised to disrupt the construction industry. Created by New York-based company Construction Robotics, a bricklaying robot called SAM100 can lay 3,000 bricks per day, effectively multiplying a typical human bricklayer’s productivity of about 500 bricks per day by six. The SAM100 (whose name stands for “semi-automated mason”) uses a conveyor belt, robotic arm, and concrete pump to lay bricks. The robot’s software ensures the robot can quickly choose between types of bricks, quickly lay bricks in complicated patterns, and strictly adhere to the building plan. However, the technology still requires a human operator to smooth the concrete before placing additional layers of bricks.
“Automation is popular in a controlled environment, but construction sites are not very controlled environments,” says Zak Podkaminer, a marketing executive with Victor, NY-based Construction Robotics. He cites weather (such as rain, snow, and humidity), space constraints, and the changing layout of the site as construction progresses as factors that can make a construction site less than ideal for automation. “There’s a shortage of skilled workers that are going into the construction trades, so what the SAM does is allow each worker to be more productive.”
Podkaminer notes that while the robot is expensive, there has been a lot of interest from contractors and masons in renting the robot, which allows it to be used by contractors that normally wouldn’t have enough work to amortize its approximately $500,000 purchase price over a longer time horizon.
Still, despite the increasing use of automation and 3D printing on the job site, the construction industry is notoriously slow when it comes to adopting new technology. This is largely due to the highly regulated nature of construction, as well as the high cost of adopting new technology, as Gardiner notes that the 3D printer used to create the massive molds can cost $1 million.
“There are inexpensive 3D construction [concrete] printers around,” Gardiner says, “but these machines are generally trading off accuracy and reliability to achieve their low cost. So, one of the things that I see is that a good concrete printer, a good construction 3D printer, will need to be highly reliable, fast, and accurate. And the problem with that is that a machine that has those things is generally more expensive.”
Gardiner, J. 2011, Exploring the Emerging Design Territory of Construction 3D printing – Project Led Architectural Research, Architecture & Design, RMIT University. https://researchbank.rmit.edu.au/view/rmit:160277/Gardiner.pdf
Building Codes, Underwriters Laboratories https://www.ul.com/code-authorities/building-code/
Laing O’Rourke’s FreeFAB Technology https://www.youtube.com/watch?v=alAHME_A8VY
SAM100 OS 2.0 https://www.youtube.com/watch?v=tK9oBQyR9KY
Join the Discussion (0)
Become a Member or Sign In to Post a Comment